Screw Air Compressor Maintenance: Key Consumables Replacement for Maximum Efficiency & Longevity
Maximize the efficiency and lifespan of your screw air compressor with regular Consumables Change Maintenance. Learn about the key components that need replacement, how often they should be serviced, and the technical & commercial benefits of scheduled maintenance. Avoid costly breakdowns and ensure uninterrupted operations with expert compressor maintenance services from Khan Contractor.
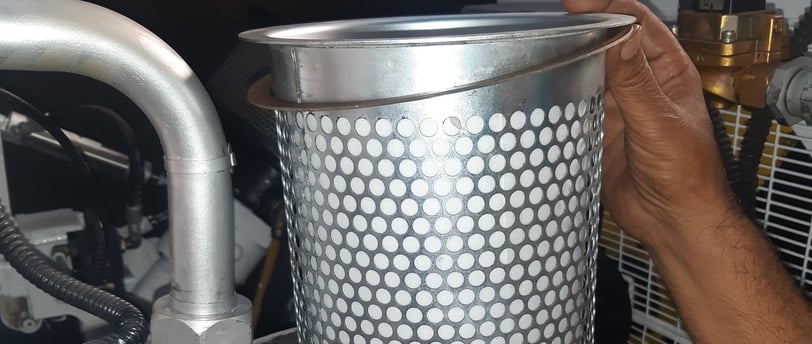
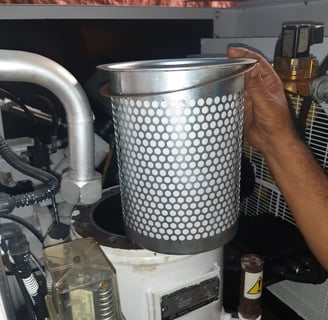
Screw Air Compressor Maintenance: Essential Consumables Replacement & Benefits
Are you looking to maximize the efficiency and lifespan of your screw air compressor? Regular Consumables Change Maintenance is the key to reducing downtime, enhancing energy efficiency, and lowering operating costs. In this guide, we break down the critical parts that require replacement, the time needed for maintenance, and the technical and commercial advantages of scheduled servicing.
What is Consumables Change Maintenance?
Consumables Change Maintenance involves replacing essential components that wear out over time in a screw air compressor. This ensures optimal performance, reliability, and energy efficiency, reducing the risk of costly breakdowns and production delays.
Key Parts to Replace During Maintenance
1. Air Filters – Ensuring Clean Compressed Air
Function: Prevents dust and debris from contaminating the air compressor.
Replacement Frequency: Typically every 2,000 to 4,000 hours, but this depends on the manufacturer’s recommendations and operating conditions.
2. Oil Filters – Protecting Internal Components
Function: Removes impurities from the lubrication system to protect key components.
Replacement Frequency: Typically every 2,000 to 3,000 hours, subject to the manufacturer’s guidelines and environmental factors.
3. Oil Separators – Enhancing Efficiency
Function: Separates oil from compressed air, ensuring minimal oil carryover.
Replacement Frequency: Generally required every 4,000 to 8,000 hours, though exact intervals vary based on operating conditions and manufacturer specifications.
4. Lubricant (Compressor Oil) – Reducing Friction
Function: Ensures smooth operation and prevents overheating.
Replacement Frequency: Typically between 4,000 to 8,000 hours, depending on the type of oil used, workload, and manufacturer recommendations.
Time Required for Consumables Change Maintenance
A complete Consumables Change Maintenance session typically takes 2 to 4 hours, depending on the compressor model, component accessibility, and technician expertise. Proper scheduling of maintenance ensures minimal downtime and sustained operational efficiency.
Technical & Commercial Benefits of Regular Maintenance
Technical Benefits:
✔ Increased energy efficiency – Well-maintained compressors consume less power. ✔ Extended equipment lifespan – Prevents wear and tear, reducing the need for costly replacements. ✔ Minimized breakdown risks – Reduces the likelihood of sudden failures. ✔ Enhanced air quality – Prevents contamination in industrial applications.
Commercial Benefits:
✔ Lower maintenance and repair costs – Prevents expensive emergency fixes. ✔ Reduced production downtime – Keeps operations running smoothly. ✔ Better ROI on air compressors – Maximizes the longevity of the investment. ✔ Compliance with industry standards – Ensures regulatory adherence and safety.
Why Regular Maintenance is Crucial for Your Business
Ignoring Consumables Change Maintenance can lead to higher energy bills, unexpected failures, and reduced compressor life. Businesses that follow a structured maintenance plan benefit from improved efficiency, cost savings, and uninterrupted operations.
At Khan Contractor, we specialize in screw air compressor maintenance services, ensuring your equipment runs at peak efficiency. Our team provides high-quality consumable parts and expert servicing for industrial air compressors.